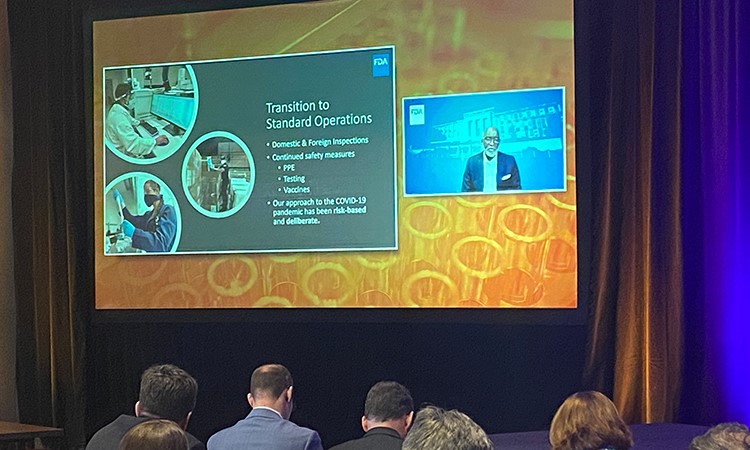
Microbial quality encompasses sterility assurance—and more, as discussed by Joyce Hansen, Vice President of J&J Microbiological Quality and Sterility Assurance at Johnson & Johnson in the keynote at the Plenary Session, “Microbiology Quality and Cultivating Emerging Leaders” that kicked off Day 2 of the 2022 ISPE Aseptic Conference.

The session was introduced by Jörg Zimmermann, Vice President, Vetter Development Service, External Affairs, Vetter Pharma-Fertigung GmbH & Co., and the 2021–2022 Chair of the ISPE International Board of Directors.
Hansen’s keynote ties together two themes: microbiology quality and cultivating emerging leaders, which have in common thinking about change. It also involves collaborative innovation, bringing in a broader audience to overcome hurdles to allow innovation.
We have inherent resistance to change in this industry due to regulatory hurdles, she said, but there are drivers that will need you to make a change
END-TO-END FOCUS

Hansen recalled a story she shared at the 2017 conference about the important of thinking with an end-to-end focus, which begins and ends with the customer. R&D, plan, source, make, and deliver are the steps in the end-to-end process. This is really about infection prevention and making sure there is no harm in products, she said.
There is need for all of these steps to be considered, Hansen said, rather than just R&D and the “make” stage and delivery to customers. There needs to be a consistent thought process of manufacturing from microbiological quality standpoint and changes have been made in J&J’s process over recent years for consistency and meeting the needs of customers.
Now we are doing microbiological quality rather than sterility assurance, she said, pointing out the change in terminology. With sterility assurance, most people only think about the “make” and “only” aseptic processing/sterilization. There was a need to change how people viewed her group because it needed to participate in the end-to-end process to deliver a good product at the end. The change of name for the group reflected this focus and gave the opportunity to explain the work of the group.
It is actually infection prevention that we do, she said; what she called the “first line of defense” (not the front line who take care of patients) to protect patients in the products. The move toward personalized medicine and potential for manufacture at bedside raises issues of how to address infection prevention in those new settings, and what microbiologic quality needs to be.
Microbial control, aseptic processing, and sterilization are all part of what Hansen calls all the tools in our toolkit that are used to achieve microbiological quality.
INDUSTRY CHALLENGES
Multiple external influences and other issues driving change in the industry include:
- Ethylene oxide (EO) emissions have come under EPA scrutiny. Operations have needed to be relocated in response to this issue, and there is pressure for the industry to move away from EO—but without it, the industry will lack capacity to sterilize. Other modalities such as moist and dry heat can be considered.
- Gamma supply disruptions are occurring due to isotope availability. This has been an issue for last two years with a 5–10% reduction, and now is being impacted by the situation with Russia, the source of 20% of isotopes.
- All manufacturers are increasing product volumes by about 10% every year.
- Timeline for R&D is shorter, as is the time between manufacture and use.
- The number of countries/notified bodies for regulatory approvals has increased.
Shifting industry strategies to address these issues needs to happen now, she said. Stop thinking of doing the same thing as always, she advised: focus on what are microbial quality needs and how to deliver?
CULTIVATING EMERGING LEADERS
Change is also affecting the pharmaceutical industry workplace, with five generations in the workforce. It can be a challenge to motivate, communicate the vision, and get them all on board with change, Hansen said.
Get people to understand the needs of all five generations: there is impact to the years of experience and up and coming generations need to be developed. Focus on technical competencies to develop those with less experience: focus on change from a “me” to “we” mindset. Leaders must think about “we” rather than individual value brought to the company.
Also focus on empowerment: give people the tools to be capable and strong and able to take on projects on their own. Coach them, guide them, and let them do the task the way they want to do it; this makes them stronger and builds future leader skills. Another focus for those moving up in the organization is the need to differentiate yourself and have your own brand.
Mentoring and coaching are also important to develop people. Mentoring is a long-term relationship where you understand what the mentee wants to do and then help them to get there (not to where you think they should be). Coaching is more project- or issue-oriented support.
Understanding career paths includes networking to build a community for ideas, skills, and passion; the latter should be part of your brand, values, interests, and ambitions.
She encouraged attendees to embrace change. “Don’t resist it, and don’t watch it around you. We have to adapt each and every day.”
ABOUT THE AUTHOR
